The quality of nonwoven fabrics can vary depending on the equipment used in the manufacturing process. Different nonwoven equipment is designed to produce different types of nonwoven fabrics, with varying properties and performance characteristics.
Here are some examples of how the quality of nonwoven fabrics can vary depending on the equipment used:
Spunbond line: Nonwoven fabrics produced using a spunbond line tend to have high strength and durability, as well as good barrier properties. The fabric may also have a smooth texture and be relatively lightweight.
Meltblown line: Nonwoven fabrics produced using a meltblown line tend to have excellent filtration properties, as the microfibers produced by the process are very fine and can capture small particles. However, the fabric may not have the same strength or durability as fabrics produced using other methods.
Needle punching machine: Nonwoven fabrics produced using a needle punching machine tend to be thick and dense, with high strength and durability. The fabric may also have a textured surface and be suitable for use in applications such as carpeting or upholstery.
Thermal bonding machine: Nonwoven fabrics produced using a thermal bonding machine tend to be lightweight and have good barrier properties. The fabric may also have a smooth texture and be suitable for use in applications such as hygiene products or packaging.
Stitch bonding machine: Nonwoven fabrics produced using a stitch bonding machine tend to have a specific pattern or design, which can make them suitable for use in applications such as apparel or home furnishings. The fabric may also have a soft texture and good drapability.
Overall, the quality of nonwoven fabrics can vary depending on the equipment used, as well as the specific process parameters and raw materials used. It’s important to choose the appropriate equipment and process for the desired properties and performance characteristics of the nonwoven fabric.
How do manufacturers ensure the quality of nonwoven fabrics?
Manufacturers ensure the quality of nonwoven fabrics through a combination of process control, testing, and quality assurance procedures.
Here are some ways manufacturers ensure the quality of nonwoven fabrics:
Process control: Manufacturers monitor and control the manufacturing process to ensure consistent quality. This may involve monitoring process parameters such as temperature, pressure, and speed, as well as inspecting the raw materials used in the process.
Testing: Manufacturers test nonwoven fabrics to ensure they meet the required specifications and performance characteristics. This may involve testing for properties such as tensile strength, tear resistance, and barrier properties.
Quality assurance procedures: Manufacturers implement quality assurance procedures to ensure that nonwoven fabrics meet the required standards and specifications. This may involve inspecting finished products for defects, tracking production data, and implementing corrective actions when necessary.
Certification: Manufacturers may seek certification from third-party organizations to verify that their nonwoven fabrics meet certain standards or specifications. Examples of certifications include ISO 9001 for quality management systems and Oeko-Tex Standard 100 for textile safety.
Customer feedback: Manufacturers may solicit feedback from customers to identify areas for improvement and ensure that their nonwoven fabrics meet customer needs and expectations.
Overall, manufacturers ensure the quality of nonwoven fabrics through a combination of process control, testing, quality assurance procedures, certification, and customer feedback. By implementing these measures, manufacturers can produce high-quality nonwoven fabrics that meet the needs of their customers.
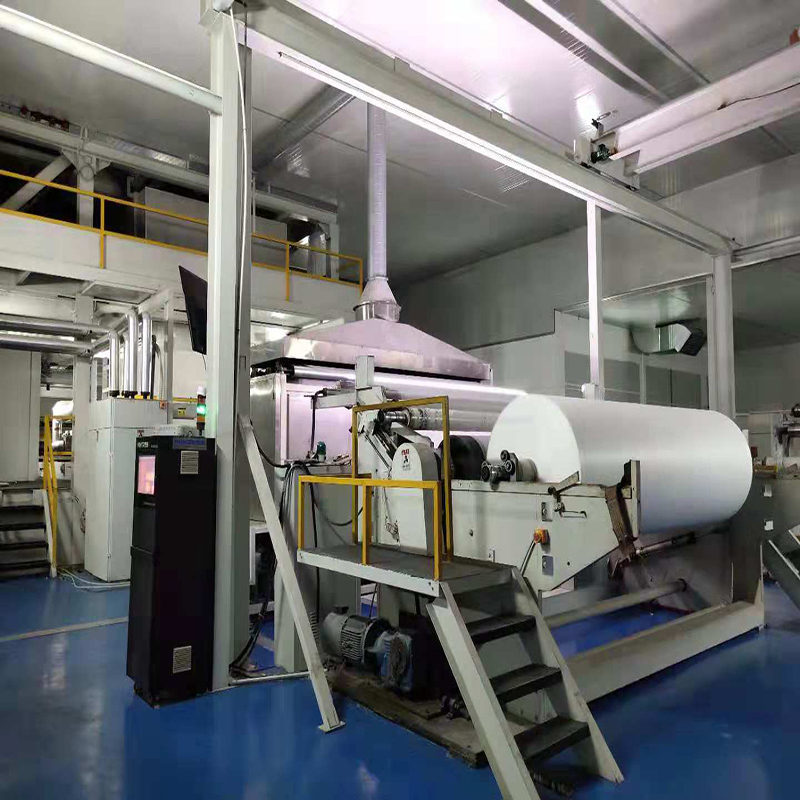