When checking the size of a pipe cross fitting, there are several measurements that need to be taken into account to ensure a proper fit.
Here are the key measurements to check:
Pipe size: The first measurement to check is the size of the pipe that the cross fitting is designed to fit. This is typically measured in inches or millimeters and is marked on the fitting itself. Make sure that the pipe size matches the size of the pipes being used in your plumbing system.
Wall thickness: The wall thickness of the pipe is another important measurement to consider. This will determine the depth of the socket that the pipe will fit into on the fitting. Make sure that the wall thickness of the pipe matches the socket depth of the fitting.
Center-to-center distance: The center-to-center distance is the distance between the center of one pipe opening to the center of the opposite opening on the fitting. This measurement is important to ensure that the cross fitting will fit properly within the plumbing system.
Angle of the cross: Cross fittings are designed to be either 90 degrees or 45 degrees. It’s important to choose the correct angle of the cross fitting for your plumbing system to ensure proper flow and stability.
Material: Cross fittings come in a variety of materials, including PVC, copper, brass, and stainless steel. Make sure to choose a fitting that is made from a material that is compatible with the pipes and fluids being used in your plumbing system.
By checking these measurements, pipe cross fitting you can ensure that the pipe cross fitting you select will fit properly within your plumbing system and provide reliable and efficient performance.
How do I measure the wall thickness of a pipe?
Measuring the wall thickness of a pipe is an important step in determining the correct size of fittings and other components that will be used in a plumbing system.
Here are the steps to measure the wall thickness of a pipe:
Clean the pipe: Before measuring the wall thickness, make sure the pipe is clean and free of any debris or residue.
Use a caliper: A caliper is a measuring tool that can be used to measure the wall thickness of a pipe. Open the caliper jaws and place them around the pipe, making sure that they are perpendicular to the surface of the pipe.
Close the jaws: Gently close the jaws of the caliper until they come into contact with the pipe. Use the locking mechanism on the caliper to keep the jaws in place.
Read the measurement: Look at the scale on the caliper to determine the measurement of the wall thickness. Make sure to measure at several points around the circumference of the pipe to ensure that the wall thickness is consistent.
Record the measurement: Write down the measurement of the wall thickness for future reference.
Alternatively, you can also use a wall thickness gauge to measure the thickness of the pipe. This tool can be placed on the surface of the pipe and provides a digital readout of the wall thickness.
It’s important to accurately measure the wall thickness of a pipe to ensure that the correct size of fittings and other components are used in the plumbing system. Using components that are not compatible with the wall thickness of the pipe can result in leaks, damage to the system, and other problems.
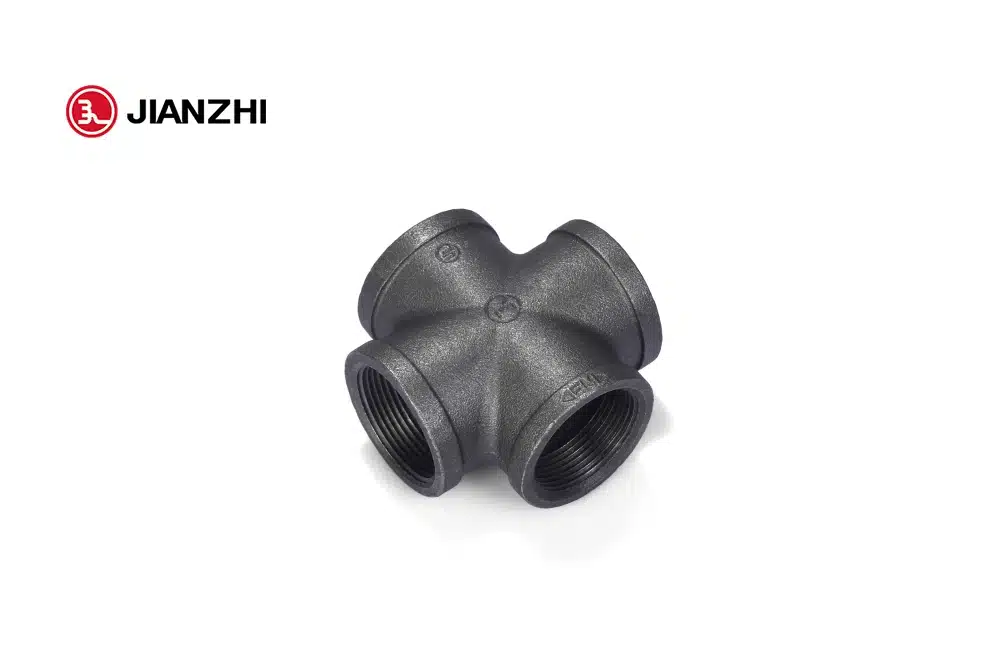