The undercarriage of an excavator plays a significant role in reducing vibration and noise during excavator operation through several mechanisms:
- Shock Absorption: Undercarriage components, such as track rollers, idlers, and track chains, are designed to absorb shocks and vibrations generated by the movement of the excavator over rough terrain. The flexibility and damping properties of these components help dissipate energy and reduce the transmission of vibrations to the rest of the machine, resulting in a smoother and quieter ride for the operator.
- Isolation of Vibrations: The undercarriage acts as a buffer between the tracks and the main structure of the excavator, isolating vibrations generated by the tracks from the cab and other critical components. By minimizing the transfer of vibrations, the undercarriage helps reduce noise levels inside the operator’s cab, enhancing operator comfort and reducing fatigue during extended periods of operation.
- Dampening Impact Forces: As the excavator performs various digging, lifting, and loading tasks, it generates impact forces that can propagate through the undercarriage and into the ground. Well-designed undercarriage components absorb and dampen these impact forces, minimizing the reverberation of noise and vibration back into the machine and surrounding environment.
- Balancing Load Distribution: Properly tensioned and aligned undercarriage components help distribute the weight of the excavator evenly across the tracks, undercarriage of excavator minimizing track slippage and excessive ground pressure. This balanced load distribution reduces the need for aggressive machine movements and mitigates the generation of noise and vibration associated with sudden accelerations, decelerations, and directional changes.
- Effective Lubrication Systems: Undercarriage components rely on lubrication to reduce friction and wear, ensuring smooth operation and minimizing noise generation. Well-maintained lubrication systems, including centralized greasing points and automatic lubrication systems, ensure that undercarriage components remain properly lubricated, reducing friction-related noise and vibration during operation.
- Vibration Isolation Mounts: Some excavators are equipped with vibration isolation mounts or suspension systems that further dampen vibrations transmitted from the undercarriage to the chassis and operator’s cab. These mounts absorb and dissipate vibrations, providing additional comfort for the operator and reducing noise levels within the cab.
- Sound-Dampening Materials: Modern excavators may incorporate sound-dampening materials within the undercarriage structure and cab interior to further reduce noise levels. These materials absorb and block airborne sound waves, minimizing noise transmission and creating a quieter operating environment for the operator and nearby personnel.
Overall, the undercarriage of an excavator plays a crucial role in reducing vibration and noise during excavator operation by absorbing shocks, isolating vibrations, dampening impact forces, balancing load distribution, maintaining effective lubrication, utilizing vibration isolation mounts, and incorporating sound-dampening materials. These features contribute to a more comfortable and productive working environment for operators and help minimize the impact of excavator operation on surrounding areas and personnel.
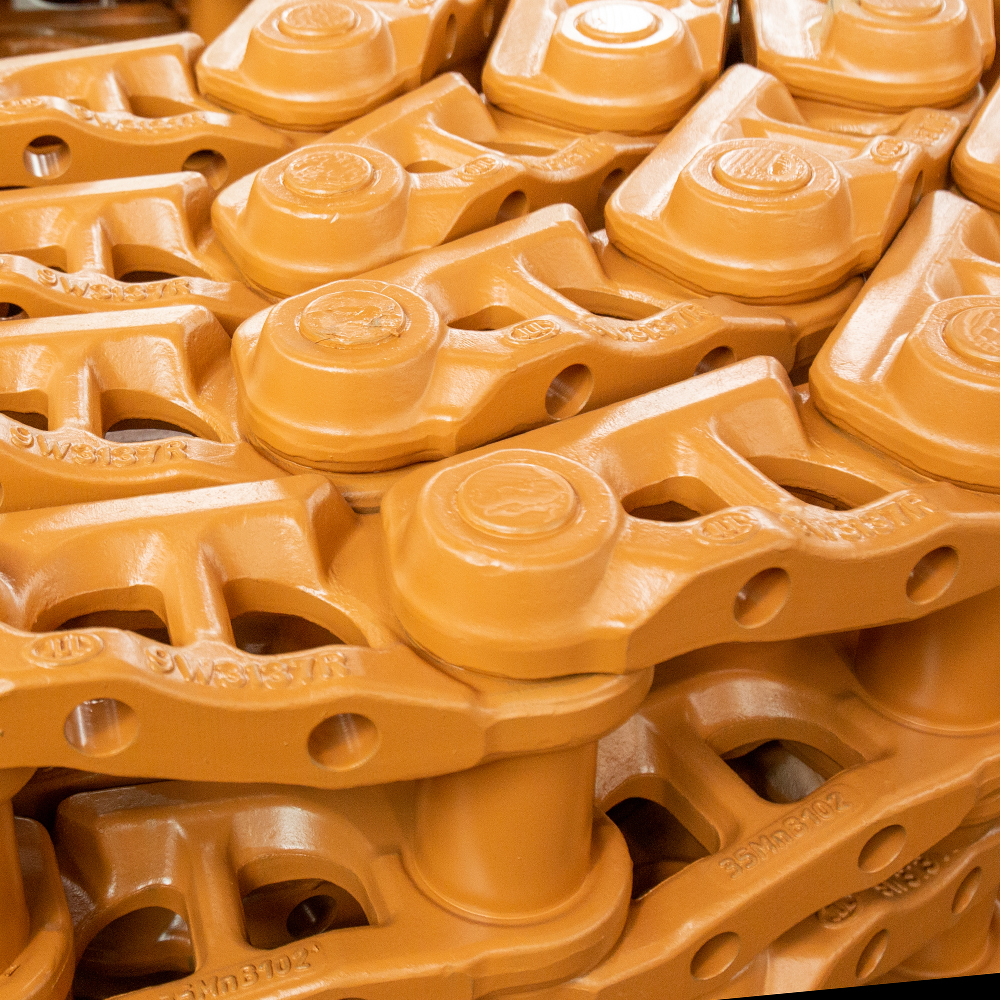