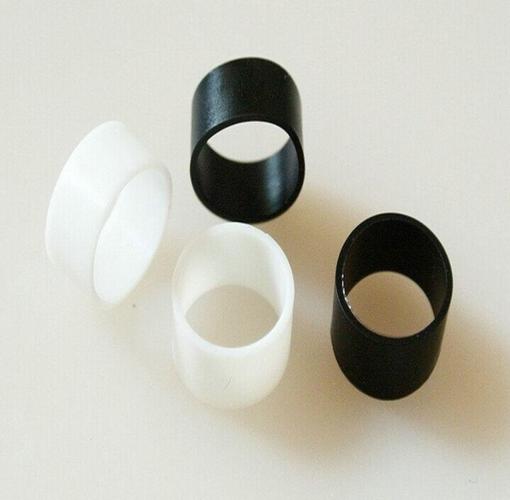
When using molded silicone to produce silicone products, the silicone products produced by low hardness silicone sometimes have cracked edges.
Edge cracking of silicone products
A, low hardness (about 30 degrees) of the rubber in the molding is easy to appear package wind (bubbles) and other bad, if the silicone body color or translucent color is also easy to see many small white dots inside the silicone products.
Solution.
The method of increasing the mold temperature, the molding of the mold temperature to increase appropriately.
Second, when the mold temperature is increased, the package wind (bubbles) and white spots bad solution, but the edge of the silicone products began to crumble, that is, the emergence of burst edge. This forms a dead-end cycle, raise the mold temperature on the burst edge, lower the mold temperature on the wind (bubble) and white spot bad.
Solutions.
- reduce the molding mold temperature, if the wind (bubbles) and white spots appear to extend the vulcanization time. Molding temperature must be fierce down until the silicone products do not burst the edge, do not think that a drop of four or five degrees of mold temperature can be solved.
- exhaust stroke and the number of times must be controlled, exhaust as few times as possible, if possible, exhaust stroke will also try to shorten.
- can be appropriate to reduce the amount of vulcanizing agent added.
Third, silicone products molding mold since the removal of the knife is too sharp or the existence of burrs.
Generally speaking, silica gel with hardness around 20 degrees is suitable for small products and fine pattern products, usually the size of these products is below 1 meter, because this type of silica gel has: small viscosity, good fluidity, good operation, easy to drain bubbles, good tensile strength, easy to fill. For large size products, usually above 1 meter in size, the hardness of the mold silicone is relatively large.
Silicone products are difficult to exhaust and shrink the edge of the cracking phenomenon
Silicone products edge (edge skin) part of the cracking, pulling the edge, shrinkage of such a phenomenon, the industry called this phenomenon for scorched edge; according to years of experience in the production of silicone products for the general scorched edge situation, that there are mainly four reasons caused by.
- The vulcanizing agent content in the rubber is too large (that is, the vulcanizing agent added more);
- Vulcanization time is too long;
- The vulcanization temperature is too high;
- The vulcanization pressure of the vulcanization instrument is too large.
There are 4 reasons for the problem of difficult exhaust of silicone products:
- The exhaust distance is too large or too short, which should be strictly controlled between 1 – 5cm;
- One exhaust is not exhausted, the second exhaust can be carried out to solve;
- Not to the vulcanization time;
- The rubber material has problems, there is moisture / vulcanizing agent dispersion is not uniform / rubber mixing is not uniform.
Silicone products exhaust difficult and shrinkage edge cracking is generally in the mold at the surface, to solve these problems, other details should also pay attention to the following
- The amount of material should also be noted;
- There is also the mold of the mold edge is not damaged, if necessary, to use oil stone polishing;
- Will there be scratch when demoulding? In the place that will be scratched to pour a little R angle;
- whether the use of poor quality silicone also has a certain relationship.
In short, different silicone products will have different problems, according to their own requirements, process, temperature vulcanization time pressure and so on how much to adjust the test